L’innovazione di Comau passa dall’Intelligenza Artificiale: ecco come le reti neurali supportano la manutenzione predittiva delle saldature
Giovanni Di Stefano, Chief Technology Officer, Comau Electrification.
Comau, società del Gruppo FCA, è un’azienda leader, a livello globale, nel campo dell’automazione industriale, pioniera nello sviluppo di processi e applicazioni avanzati di saldatura laser. Conta ad oggi 9000 dipendenti, 8 stabilimenti di produzione in 14 Paesi, 7 centri di innovazione e 5 digital hub, e vanta laboratori laser altamente specializzati nell’implementazione e nell’ottimizzazione dei processi laser che riguardano la costruzione e l’assemblaggio di motori e batterie elettrici. Tra i diversi settori in cui opera, Comau si muove anche all’interno di un’industria, quella dell’automotive, che copre una fetta importante dell’utilizzo della robotica a livello mondiale, in cui diventa strategica la raccolta e la correlazione di dati. Il tema dell’automazione, inoltre, è tra i più “caldi” nell’agenda della trasformazione digitale e del lavoro nelle aziende: “Per noi l’automazione industriale non rischia di togliere il lavoro all’operatore, piuttosto permette un upskilling di quest’ultimo e il miglioramento della qualità del prodotto; abilita il passaggio a un lavoro più qualificato e più qualificante e l’opportunità per le aziende di innovare”, spiega Giovanni Di Stefano, Chief Technology Officer di Comau Electrification. Comau ha effettuato saldature per 45 anni dandosi come obiettivo principale la garanzia della performance meccanica. Ora, con l’avvento delle batterie elettriche per auto, l’azienda torinese ha avviato un progetto con l’obiettivo di garantirne anche la performance elettrica. “Il progetto si inquadra in una più ampia rivoluzione all’interno dell’azienda, che mira da un lato alla digitalizzazione delle diverse tecnologie, dall’altro ad affrontare il rinnovamento del proprio catalogo prodotti, per rispondere alle esigenze delle imprese clienti, sia nel campo della mobilità tradizionale che di quella elettrica”, sottolinea Di Stefano. I controlli tradizionali, per i comportamenti elettrici e meccanici del giunto, sono basati sul riscaldamento in camera stagna e successiva ispezione della curva di raffreddamento con una termocamera. “Poiché questo processo risultava oneroso in termini di impegno economico e temporale e anche perché molto complesso nella sua realizzazione, abbiamo avuto l’idea di scaldare il giunto con lo stesso laser con cui effettuiamo la saldatura, monitorando poi con la termocamera i comportamenti termografici”. Forti della collaborazione avviata con il Politecnico di Bari già nel 2016, con il quale era stato sviluppato un sistema di visione di random bin picking (un robot che estrae oggetti random), ad agosto 2019 l’azienda ha creato a Bari un team altamente specializzato, dedicato all’image processing e a reti neurali artificiali e ha dato vita a MI.RA (Machine Inspection and Recognition Archetypes). “Proprio una delle famiglie di tecnologie di MI.RA è la termografia (MI.RA/ Thermography): avevamo infatti capito che, per determinare proprietà meccaniche ed elettriche di ogni singola saldatura, dovevamo attingere a sistemi di misura non convenzionali”, spiega il manager. È stata quindi realizzata una prima analisi di fattibilità su 1.000 giunti ed è stato sviluppato un software basato sulla capacità delle reti neurali artificiali di fare forecast; il sistema dà i propri feedback sull’interfaccia uomo-macchina, fornendo grandi quantità di dati che permettono di fare manutenzione predittiva e di scartare il solo giunto difettoso, integrando l’intero processo con il flusso logistico. “Uno dei principali problemi che abbiamo dovuto affrontare in questo progetto è stata proprio la capacità di correlare i dati e di trasmettere la conoscenza del processo. Non abbiamo invece avuto problemi nel trovare software engineer esperti delle reti neurali, anzi da questo punto di vista l’Italia è molto competitiva”, commenta Di Stefano, che aggiunge: “altro elemento critico è stato il tempo, perché questo tipo di progetti è ancora sperimentale: non sai quanto tempo impiegherai a sviluppare un prodotto del genere, che richiede tecnologie costose. Quando pensi di aver finito, devi fare ottimizzazioni, per esempio utilizzando il deep learning o il machine learning. Per questo motivo non è facile proporlo internamente o esternamente”.
Siamo a tua disposizione per informazioni e assistenza
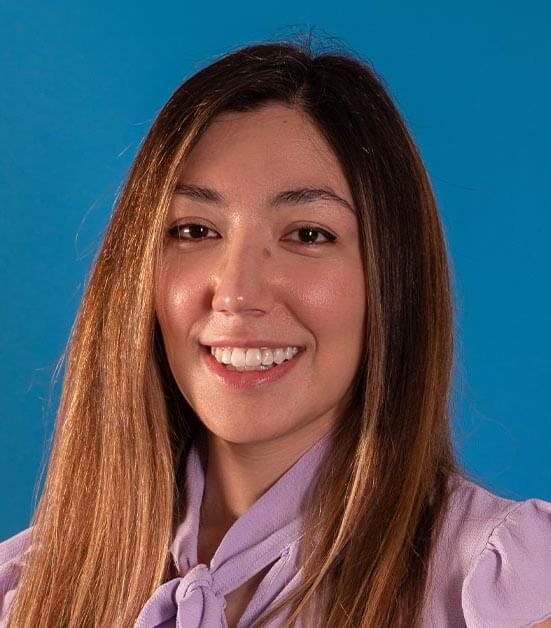
Martina Vertemati
Acquisti e abbonamenti Da Lunedì al Venerdì, dalle 09 alle 18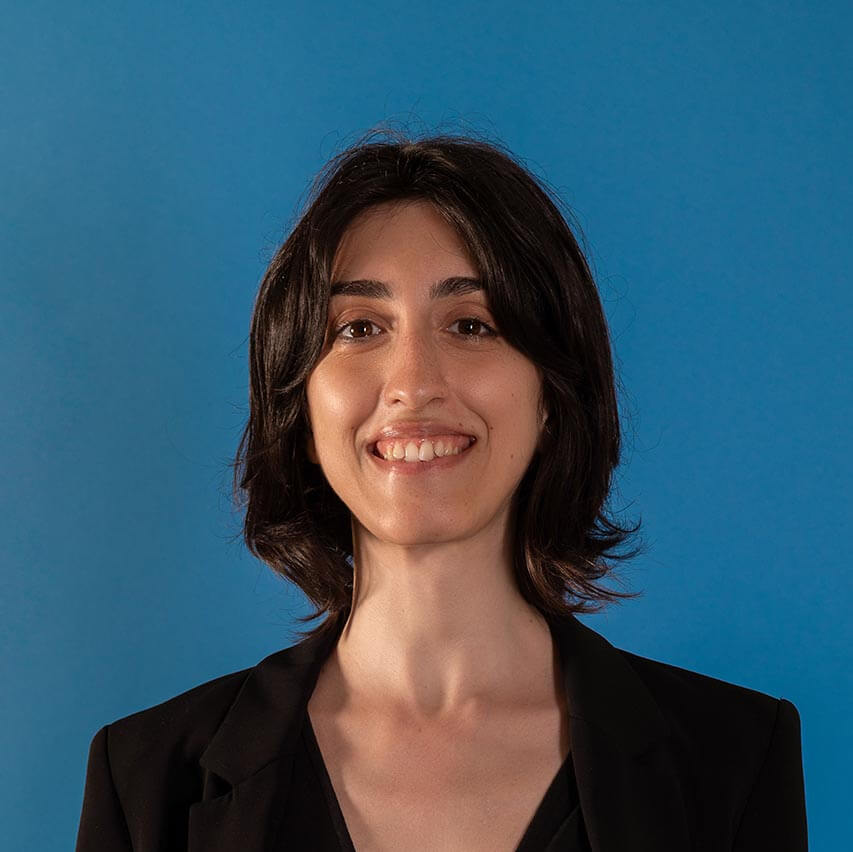
Alessia Barone
Assistenza Da Lunedì al Venerdì, dalle 09 alle 18Scopri altri contenuti di Startup Thinking

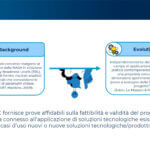
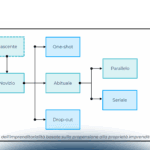
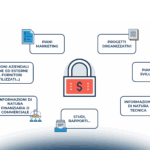
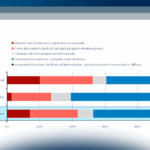
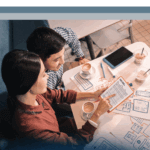
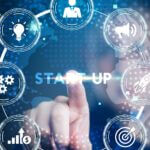
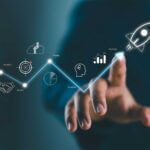
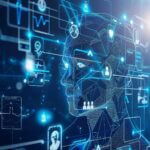
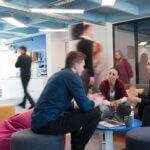
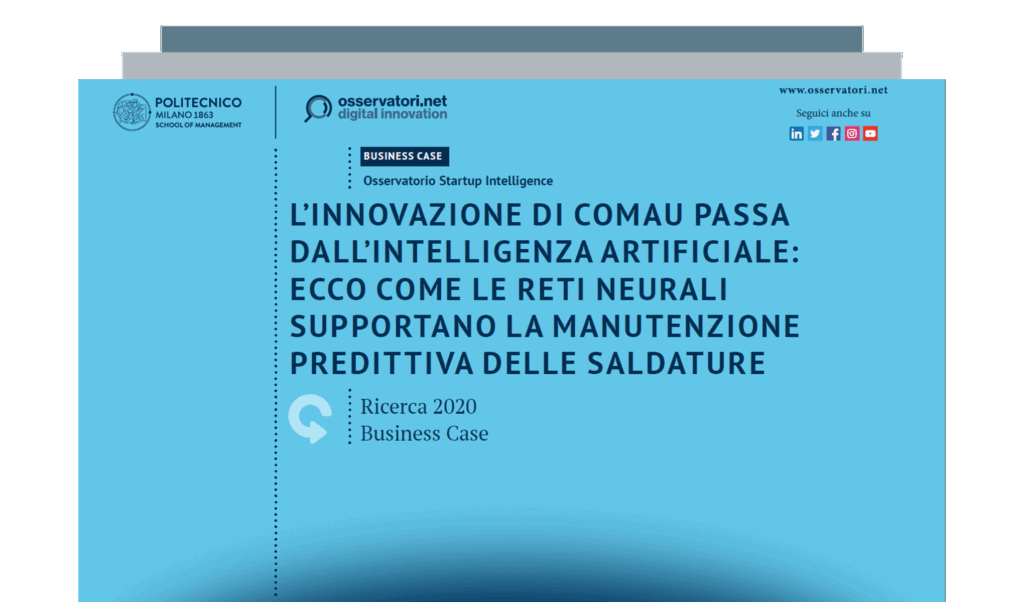